Investment Casting
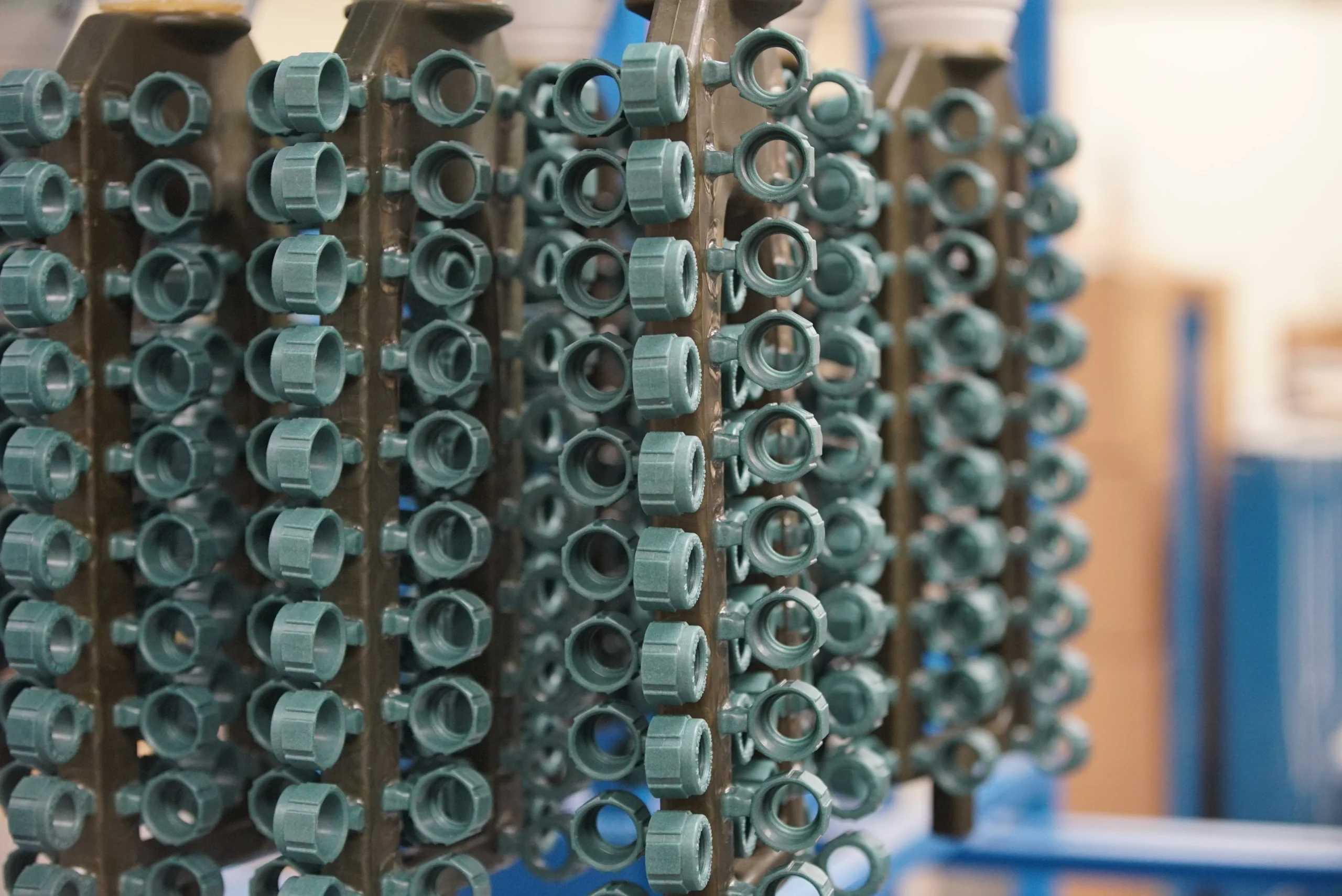
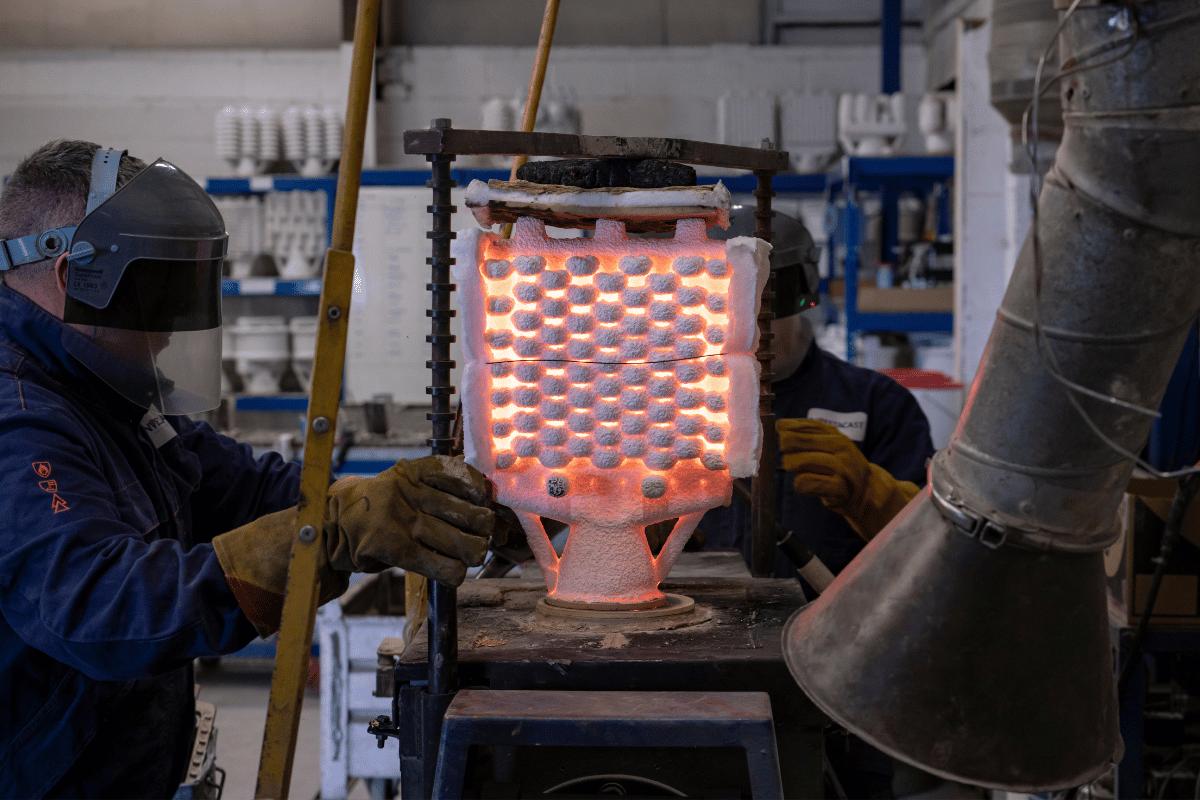
- Investment Casting
What is Investment Casting?
- Pump & Valve Components
- Vehicle Components
- Turbocharger Impellers
- Machinery Components
- Parts with Complex Geometry
- Food & Beverage Grade Machinery Components
- Misc. Equipment Parts
- OUR PROCESS
The Investment Casting Process
1. Engineering Review
The first step begins with a thorough customer evaluation of the Design for Manufacturing (DFM).
5. De-Waxing
The shell containing the wax pattern is placed into an autoclave that uses steam heat and extremely high pressure to remove the wax.
2. Mold Design / Build
Once the initial evaluation is complete, we precision-engineer a wax injection mold that can be used to produce wax patterns for the final part.
6. Foundry & Pouring
The mold is placed into a high-temperature oven set to approximately 1000 C (1832 F) for curing and to prepare it for accepting molten metal.
3. Wax Pattern Production
The wax injection mold is sent to the wax room for injection and assembly, defining the required production capabilities.
7. Shell & Casting Removal
Once the metal has cooled, the ceramic mold shell is broken away. At this point, the casting(s) can be removed from the metal tree.
4. Ceramic Mold Construction
We dip the wax tree into a ceramic slurry until it is completely enveloped in the material. The tree is then thoroughly coated in sand to create a shell that forms the first layer. The mold is then dried.
8. Finishing
he part’s gate is often removed by machining or grinding after manufacturing. Investment castings utilize a ceramic mold that can produce a much smoother surface (averaging a 125 RA surface finish).
- Benefits
Benefits of Investment Casting vs. Other Methods
- Economical tooling options
- Elimination of machining in many cases
- Smoother finish
- Tighter tolerances
- Ability to cast complex geometries
- Wide variety of materials
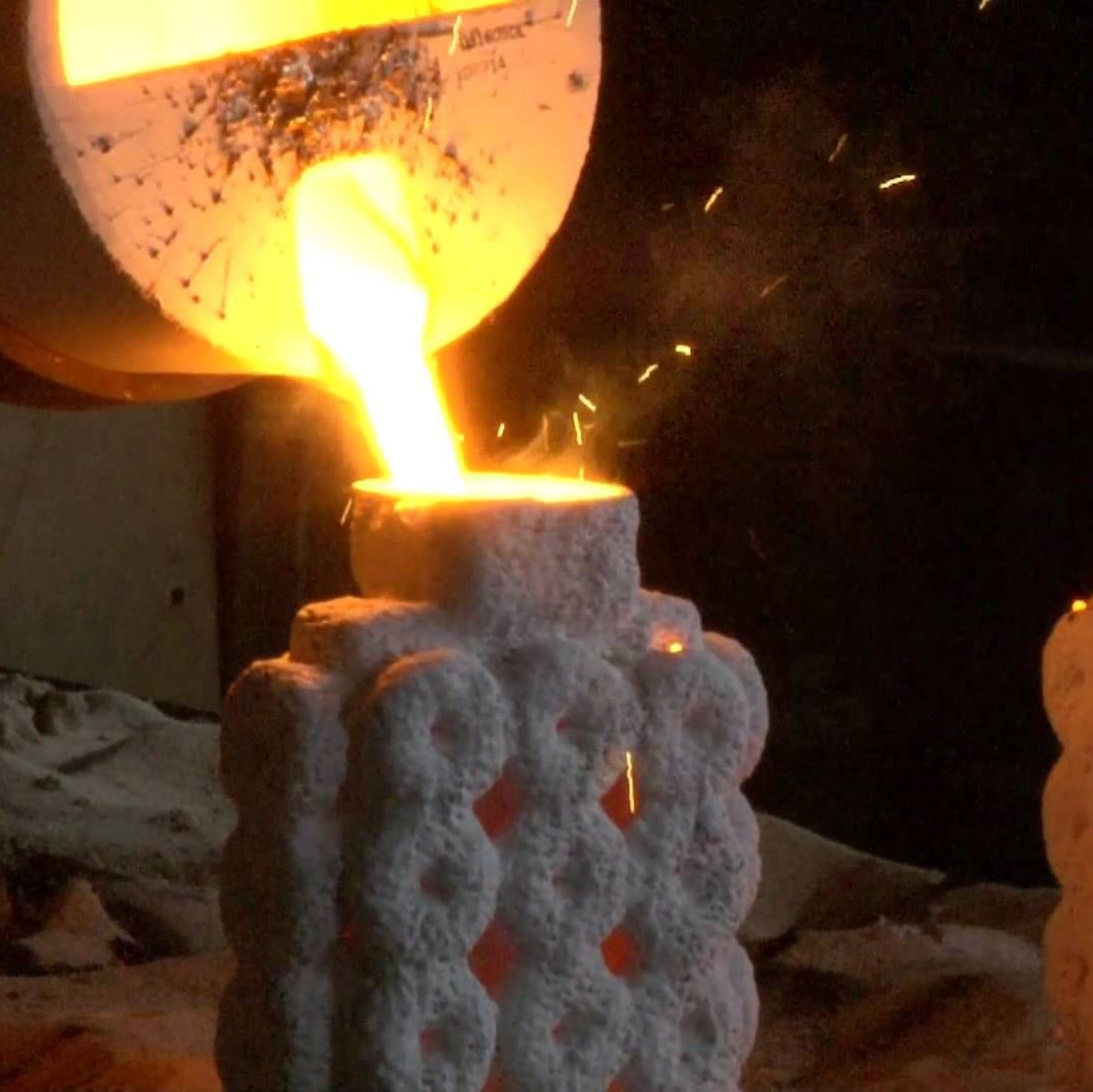
Materials
- Stainless steel
- Alloy Steels
- Haynes
- Incoloy
- Inconel
- Rene
- Aluminum
- Cobalt Alloy
- Carpenter 20
- Tool Steel
- Monel
- Nickel Alloy
- Waspaloy
- Hastelloy
Dimensions
- Less than 1″
- Up to 24″
Tolerances
- ±.003”
Lbs. Per Casting
- Ounces to 75 lbs.
Volume Capacity
- 100 to 100,000
Industry Focus and Intended Applications
- Aircraft & Aerospace
- Oil & Gas
- Road Construction
- Coal Mining
- Steel Production
- Steel Processing
- Heat Treating
- Off-Road Equipment
- Valve & Pump
- Railroad
- Propane Tank
- Food Equipment
- Thermal Processing
- Heavy Truck
- Glass
- Fiberglass
- Porcelain Enameling
- Power Generation
- Marine
- Bearing
- Forging
- Foundry
- Industrial Furnace
- Industrial Shredder
- Fastener
- Turbocharger
- Material Handling
- Wind Power
- Agricultural Equipment
- Pharmaceutical
- Chemical Processing
- Petrochemical
- Cement